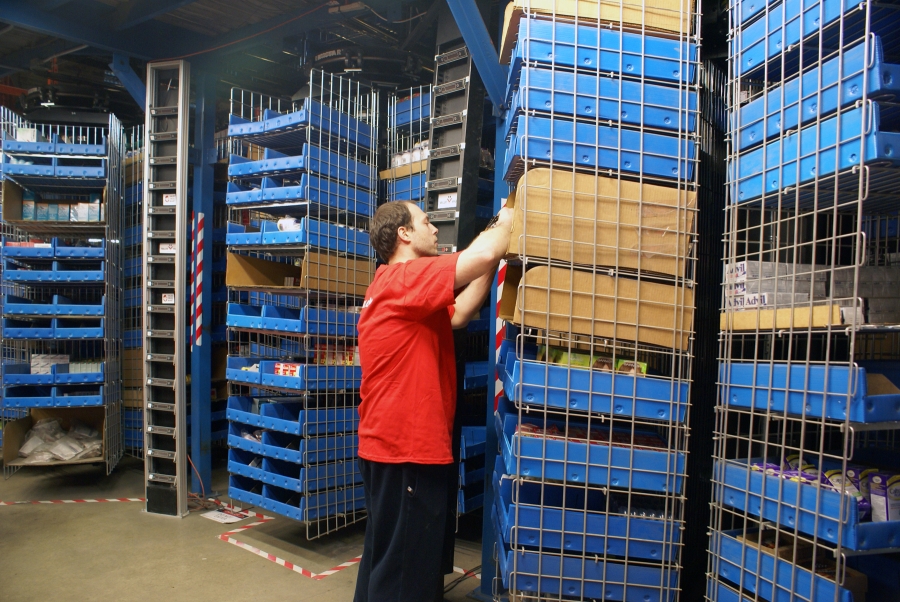
Value Drug Mart Adds Value To The Supply Chain
In 1978, thirteen pharmacy owners centralized their purchasing and distribution power to compete with the big chains, while still maintaining the spirit of independent ownership and community focus that neighborhoods had come to depend on. Today, there are 32 member shareholder stores under the Value Drug Mart banner, as well as 11 Apple Drugs stores, 8 Rxellence Professional Dispensaries, and approximately 300 affiliated stores—all served by a central distribution center in Edmonton, Alberta.
The Value Drug Mart distribution center distributes front store items (everything from bedding and soap to pantyhose and chapstick) and pharmacy items; keeping the tradition of locally-owned, community-minded service alive and well throughout Alberta and British Columbia.
With shareholder stores needing to expand their front store offerings to remain competitive, changes would also be required in their distribution center to better manage the cube. Orders for front store items were increasing rapidly and new growth presented challenges on several fronts. The 85,000 square foot distribution facility has a 60,000 square foot warehouse that manages 18,000 SKUs spread over multiple pick zones that included pallet rack, flow rack, standard shelving and bulk areas. “We couldn’t hire fast enough to keep up with the growing demand,” said Dwayne Bilawchuk, Operations Manager.
An Automated Solution
To meet increased demand, Value Drug Mart replaced two zones of static shelving with 6 horizontal carousels integrated with pick to light technology from Kardex Remstar. The horizontal carousels were stacked and arranged in two zones of 3 carousels, each zone with an 8 position batch. Bilawchuk has since added two additional picking positions, which would allow for 10 orders to be picked at a time, further increasing pick productivity and order through-put.
Faster Picking… Much Faster
The previous shelving consisted of 2 levels of mezzanine, with front store items stored on the top level and pharmacy items on the bottom level. It was a paperless picking environment. Workers wore pick aprons and used remote scanners, traveling up and down aisles to fulfill orders. Software was in place to provide logical picking sequences. “We were picking as fast as staff, shelving and technology would permit, but it wasn’t fast enough,” said Bilawchuk.
All 10,000 SKUs were moved from the 2 shelving zones into the 2 horizontal carousel zones. The lower carousel zone manages 3,100 front store SKUs with an average pick rate of 350 lines per hour. The upper carousel zone manages 7,100 pharmacy SKUs and boasts a pick rate of 575 lines per hour. With a previous pick rate of 50 lines per hour from shelving, these two zones are averaging a 90% faster pick rate!
Less Labor
Not only are orders picked faster, but the labor required has been reduced by 72%. The shelving zones required 3 people for 6 hours per day to manage each zone. Each horizontal carousel zone is managed by 1 person working a 5 hour shift. Reducing the total number of man hours for both zones from 36 hours per day to 10 hours per day of picking.
Space
The previous shelving zones occupied 3,900 square feet on each level. All SKUs were moved from the mezzanine shelving into the 6 horizontal carousels, stacked to create 2 zones. Each carousel zone now occupies 1,625 square feet on each level, saving 2,275 square feet of floor space- a 58% space savings! The recovered floor space is now used for bulk goods storage, much of which was previously stored in an offsite location.
Scanning For Accuracy
A scanner, similar to a retail check out scanner, is mounted at each end of the batch station. Before each item is placed in the order tote it is scanned for accuracy verification. The consolidation area spot checks orders for accuracy. “Our order accuracy has always been high, these measures help us maintain near perfect pick accuracy,” says Bilawchuk.
Facility Flow
Shareholder stores place several orders throughout the day. Orders for each store are consolidated into one order before they are sent through to the warehouse for fulfillment. This allows the distribution center to pick one order per store, but invoice it as the multiple orders that were placed.
The distribution center is divided into 28 zones (9 flow rack zones, 5 bulk picking zones, 12 shelving zones and 2 horizontal carousel zones). Using a parallel picking strategy, each order is divided up among the zones based on the SKUs the order requires. Each zone fulfills the order with the SKUs from that zone and sends the partial order to consolidation.
All SKUs required from 6 of the 9 flow rack zones are filled using a pick and pass strategy. Orders are picked from one flow rack zone and passed to the next flow rack zone until all of the SKUs required are collected. The other three flow rack zones are processed independently. Like all other zones, the flow rack SKUs are then sent to consolidation to meet up with the rest of the required SKUs that will complete the order.
Orders requiring SKUs from the horizontal carousel zones are sent through an interface from the company host computer to the Nova inventory management software that manages both carousel zones. The horizontal carousel operator first assigns a shipping tote to a location on the batch station, each tote represents an order. The operator can fill up to 10 orders at one time. With the push of a button the 3 carousels spin to retrieve the first and subsequent SKU’s to be picked.
Using pick to light technology, the operator is directed to the exact cell to pick from within the horizontal carousel. The light tower displays the quantity to pick. The operator picks the quantity required and turns to distribute them among the orders on the batch station.
Each position on the batch station is also fitted with a put light. This displays the quantity to put into each order tote. Before placing the SKU into the tote, the operator scans the SKU for accuracy using the scanner mounted at each end of the batch station. When the SKUs have been distributed among the orders, the operator pushes a confirmation button.
While the operator is distributing the SKUs among the orders, the next horizontal carousel has positioned itself for the next pick, virtually eliminating operator wait time. The operator simply turns back to the 3 horizontal carousels and the pick to light technology directs them to the next pick. The operator continues to pick from the carousels and distribute the SKUs among the orders until all SKUs for each order have been picked.
Completed orders are sent from each horizontal carousel zone via conveyor to the consolidation area where they are held until the rest of the SKUs required for the order arrive from other zones. Once all SKUs required for an order arrive at consolidation they are matched and forwarded via conveyor to shipping.
Managing Seasonal Growth
In the fall, Value Drug Mart manages a back to school program allowing schools to preorder supplies for children. Value Drug Mart provides the school one order per child with the supplies requested by the school. “This is a growing seasonal program that we would not have been able expand without the addition of the horizontal carousels,” said Bilawchuk.
Kardex Remstar, LLC, a company of the Kardex Group is a leading provider of automated storage and retrieval systems for manufacturing, distribution, warehousing, offices and institutions. For information about our dynamic storage solutions, call 800-639-5805 or visit www.kardexremstar.com.