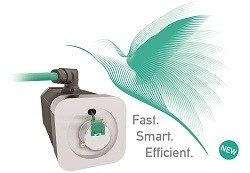
Posital - Multiturn Kit Encoders
MULTITURN KIT ENCODERS WITH BISS LINE INTERFACE
Now with the Open Source One-Cable-Technology BiSS LINE:
POSITAL’s new family of kit encoders provide the manufacturers of motors and other machinery with rugged, accurate and cost-efficient tools for building rotary position feedback into their products. The new kit encoders are based on POSITAL’s highly successful self-contained magnetic rotary encoders. Now however, the core components of these instruments are available as separate assemblies that can be readily integrated into other products.
• Asynchronous RS485 Interface, 4-Wire Configuration
• Open Standard: BiSS Line
• Smart Multiturn – Wiegand Technology – No Battery, No Gear!
• Compact Single PCB Design
• Auto-Calibration – No Mechanical Adjustment
• Insensitive to Dust and Moisture
Non-Proprietary Interfaces Reduce Costs, Increase Versatility:
The electronic interface for these encoders is based on non-proprietary BiSS Line and BiSS-C communications standards . Unlike proprietary, vendor-specific interfaces, these open-source standards are be supported by many manufacturers of sensors and motion controllers, freeing users from a “locked-in” relationship with a single supplier. Standard 4-wire RS485 connections are supported, so that motor manufacturers who adopt POSITAL kit encoders can often make use of existing connectors and cables. IP core software is available for FPGAs widely used in motion controllers. This reduces the development effort required to make use of BiSS communications technologies.
The BiSS Line standards also support a single cable approach to motor connections, with power and control wires combined in a single cable. Point-to-point or multi-slave network configurations are supported, simplifying wiring layouts in complex machines.
High Performance with Low Maintenance:
The POSITAL kit encoder components offer advantages for motor and rotating equipment control feedback. Compared to analog resolvers, they provide improved accuracy and multiturn measurement capabilities. Their output is digital, which avoids the need for A/D converters in the control system. Compared to optical disk encoders, POSITAL’s magnetic encoders are less costly, less vulnerable to contamination from oil or dust and more resistant to shock and vibration. Multiturn absolute position measuring capability is based on an electronic rotation counter powered by the company’s well-proven Wiegand-effect energy harvesting technology . This system is self-powered, so rotation counts are always accurate, even if rotations occur when there is no control system power available. With no need for backup batteries and no need for periodic backup battery checks and replacements, maintenance requirements are significantly reduced.
Efficient Installation:
POSITAL magnetic kit encoders are easy to incorporate into normal manufacturing processes since they don’t require near-cleanroom assembly conditions. A built-in self-calibration capability can be used to compensate for small sensor-to-shaft alignment errors occurring during assembly. The electronic components, including Hall-effect sensors, a 32-bit microprocessor and the Wiegand-wire energy harvesting system, are packaged in a convenient 36 mm diameter, 24.2mm deep unit. For servomotors with magnetic brakes, a special magnetic shield can be installed to isolate the magnetic pickups from external magnetic fields.
The resolution of the new POSITAL kit encoders is 17 bit, with an accuracy of better than +0.1°. The operating temperature range is -40 to +105 °C.