Automotive Service Departments Plan For Service And Maintenance Growth
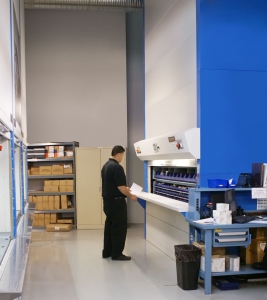
Automotive Service Departments Plan For Service And Maintenance Growth
As consumers gain confidence and return to showrooms, parts and maintenance departments are planning for the added service and maintenance work that follows sales growth.
In order to maximize service profit associated with the steady increase in car and vehicle sales, dealerships and service centers are looking for ways to increase service technician efficiency, improve customer service and reduce the costs of operations. Very often a change or reorganization in parts operations can make a big impact on the overall bottom line of the service center.
Increasing Service Technician Efficiently
Service technicians waiting around for parts are not productive and they cost the service center money. The ability of the parts department to get parts to technicians in a timely manner impacts overall customer satisfaction and service center profit. Most service centers, while recognizing the importance of efficient parts department operation, often don’t evaluate different approaches to parts storage and retrieval operations and consequently don’t use the most effective storage medium for those operations. The right combination of equipment and process can significantly improve the efficiency of parts storage and retrieval operations and improve space utilization, productivity and efficiency in the service center.
In a typical parts operation, service technicians walk to the parts counter to place an order and wait for the counter person to locate and retrieve the part. The wait time is valuable time not being spent in the service bay. One approach to more efficient parts storage and retrieval is the installation and integration of automated storage and retrieval systems. Automated storage and retrieval can improve the efficiency of wholesale and retail counter operations as well.
Conventional static storage systems like shelving and bins require order pickers to spend much of their time traveling aisles searching for items. Automated storage and retrieval systems allow quick access to goods via a system of rotating shelves that bring the exact pick/store position to the operator. These systems can be installed in as little as a week and run thousands of hours between scheduled maintenance periods. They have the advantage of significantly improving the efficiency and productivity of parts picking, up to 60% in some applications, while offering a more accurate method of maintaining inventories and reducing mispicks. In doing so, they increase technician billing efficiency and counter staff productivity, reduce inventory levels, and improve customer service and satisfaction.
With an automated system the technician can order the part from a terminal located at the service bay. The order is received instantly by the service department, the parts required are retrieved and a runner then delivers the part to the service technician at the service bay. This virtually eliminates waiting time and keeps the service technician at the service bay, servicing vehicles.
Automated systems, such as Kardex Remstar vertical carousels and Shuttle® vertical lift modules (VLM), take advantage of unused overhead space, effectively reducing the amount of space required for drawers, bins, rack and shelving and bulky bin storage areas, recovering up to 85% of the floor space required by these devices. Recovered space can often be used to create more service bays or showroom areas. Improved space utilization also extends the useful life of existing facilities, eliminating the need for expensive building expansion projects.
Trays and carriers and can be configured to hold a variety of bin sizes, allowing the efficient storage of parts ranging from small fasteners to special tools and larger parts. Automated systems are particularly suitable to kitting applications where several part numbers must be picked as a unit for a particular end use, such as an oil change for a specific vehicle model.
Automated storage and retrieval systems provide 100% accessible storage and are designed to deliver stored items at an ergonomically optimized height to eliminate bending, stretching and reaching. Operators simply enter the part name or number into the system and stored items are automatically delivered to the operator, eliminating walk and search time to reduce labor requirements by up to 66%. This ergonomic design not only improves productivity, but also reduces employee stress and injury.
Inventory Control Plus Picking Efficiency
When vertical carousels and VLMs are integrated into an existing inventory control system, inventory levels can be managed more accurately and cost effectively and parts retrieval speed can increase significantly. FastPic Auto inventory management and control software from FastPic Systems can be interfaced with proprietary automotive inventory control software to assure optimum inventory levels. As a certified integration partner for both ADP and Reynolds & Reynolds, the software provides seamless two-way exchange of order information, receipts, cycle count transactions, pick, put and return data, part and kit numbers, and other inventory information between the host system and FastPic software. More precise inventory control results in enhanced productivity and order processing efficiency, reduced item handling and improved billing and inventory accuracy.
Vertical storage and retrieval systems also offer increased picking speed and accuracy using position indicators and information displays that direct the counter person to the precise location of the stored item, significantly improving throughput.
Measuring ROI
An automated storage and retrieval systems represents a significant capital investment, but the cost savings can be substantial, and the return on investment can be as short as 12 months. How to determine if an automated storage and retrieval system is an appropriate investment? Sit down with an installation specialist and put the numbers to the test. A standard ROI/IRR (Return On Investment/Internal Rate of Return) can calculate the daily cost of the current system and compare it to the daily cost of the new system. It also provides the dollar savings from reduced space requirements, cost savings from improved employee productivity, depreciation savings and total annualized savings. From this information, you can determine the payback schedule for the specific installation.
Now that vehicle sales are starting to increase, automotive dealerships should prepare themselves to take advantage of the after sales profits by exploring the benefits of automating their parts storage and retrieval operations.
Kardex Remstar, LLC, a company of the Kardex Group is a leading provider of automated storage and retrieval systems for manufacturing, distribution, warehousing, offices and institutions. For information about the utilizing our solutions in parts and service departments, call 800-639-5805 or visit www.KardexRemstar.com.